CNC (Including Swiss Screw) Machining vs. Injection Molding, Which is the Right Choice?
- By kensmith
- •
- 07 Dec, 2018
- •
Since I just got back from the BioMedevice Show in San Jose, I thought a post is warranted since I spoke to a lot of injection molding companies while I was there.
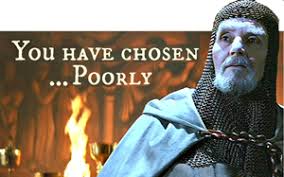
Where do I even start....
When talking with some of my customers that we machine parts for, the path is always the same...R & D components (maybe 5), then several iterations (maybe up to 5; which may/may not require prototypes), then small production run (100-500), then larger production runs (500-5000/yr) and then increasing as the product continues its life cycle and gains familiarity in the market then then at some point, the conversation comes up about switching to injection molding instead of continuing machining them (insert audible record player needle scratch!).
When moving from design to creating your parts, you must decide how to make the parts. In the best-case scenario, you had already considered this during the design process and your design is already optimized for one of the processes. Keep in mind, during the development life cycle; the right choice MIGHT change. Two common methods I want to talk about are CNC Machining (Including Swiss Screw) and injection molding. Both have advantages and disadvantages when choosing between them.
Before I get started, let me preface this blog with CrossWind Machining is a CNC Swiss Screw Machine shop, WE DO NOT and HAVE NOT
done injection molding but I/we do understand the nuances of both processes pretty well. This post is NOT about advocating for one or the other process, only you can determine which is right for you. But rather laying out the nuances of each that will help you make your decision to go with either (or both!) processes.
First of all, if you've gotten your production to the quantity levels to even consider injection molding, bravo to you! However,just because that's what the industry considers the standard progression in manufacturing, it isn't always the answer... just like in Indiana Jones when the knight protecting the Holy Grail is making them choose a “cup” to drink from - a word of caution....Choose Wisely!
Now let’s get started and look closely at each process!
CNC (Including Swiss Screw) Machining:
A process that typically starts with a block or bar of the desired material. CNC machining involves precisely removing material layers at a time. This process allows for many different materials to be used with few limitations. Also, because it is computer controlled, very precise tolerances can be achieved.
Injection Molding:
As the name suggests, this process involves injecting material into a mold. This is done by melting the stock material and forcing it into mold at high pressure. The part is then allowed to cool in the mold and then is ejected from the mold. The process is repeated for the next part.
Which process is right for you?
In general, this can be looked at as a trade-off between multiple of different characteristics; speed, volume, material, tolerances/surface finish, and design. Each one of these can be a limiting factor in using one process vs. the other and might even require changes to the part in order to manufacture.
Speed:
This is the simplest. For low volume of parts, CNC machining is the fastest. If you need 10 parts in 2 weeks, CNC machining is probably your only solution. If you need 50,000 parts in 4 months, injection molding can be the way to go. Injection molding requires time to make the mold and ensure the parts are in tolerance. This can take anywhere from a few weeks to several months. Once this is done, creating parts using the mold is a very fast process. The upfront time & cost investment of injection molding will pay off at high volumes….
Volume:
Let’s look at this independent of time. Instead, the focus here is price per part. Which are cheaper changes depending on volume. CNC is cheaper when you need a few parts up to a few thousand. While you do get some benefit of volume in the price, it is typically seen between a few parts and a hundred. At larger volumes, you do not get any additional benefit of volume. This is from distributing the setup cost over the number of parts made + material needed.
The actual cost per part of injection molded parts is significantly cheaper that machined parts. Unfortunately, for injection molding, the creating the mold can be a large upfront cost. This is than spread out across the number of parts made to determine the cost per part. At a certain volume, even with the large upfront cost of the molds, injected parts become cheaper than machined. As more parts are created, the gap in cost becomes greater. This crossover can occur from as little as 1000 parts up to about 5000 (but there usually is many factors that dictate this).
At least to some degree, asking what plastic injection molds cost is a lot like asking “How much is a car?”. Will your mold be a Pinto or a Porsche? Features? Complexity of the mold? You get the picture....
According to Rex Plastics, "the determining factors in the cost of your mold are a combination of the part size, complexity, material, and anticipated quantities. For instance, if you wanted 1,000 washers per year, we would recommend a single cavity mold, meaning it makes one washer per machine cycle. In that case the mold would probably be $1,000-2,000."
"On the other hand, if you are going to need 100,000 xbox controllers every month, we would build a 12 cavity hardened “family” mold which made four Fronts, four Backs, and four Button Trees every cycle, and you’d better have $60-$80,000 or more to invest."
"Of course these examples are extreme, but it illustrates the range of costs to anticipate. Your particular part will most likely fall somewhere in between that, and the molds that Rex Plastics builds average around $12,000."
"Material selection is another consideration in determining what plastic injection molds cost. If your product requires a fiberglass filled material for instance, it will most likely need a mold made from hardened tool steel due to the wear those materials cause when being injected under high pressure."
"If you have a target price established for your parts, it will be helpful to let your mold builder know that, because they can design the mold with that in mind, and plan for the right number of cavities to achieve that price. The more cavities (or parts made per cycle), the less expensive the parts will be, also allowing for higher output."
"While you don’t need to know every detail about the types of molds available, it’s always a good idea to come prepared. Supplying the basics to your mold builder will help them build the best tool for your project. It’s also recommended that you find a mold maker who also has production capabilities. The company running the production won’t want to build an inadequate mold because they know they have to use it!"
Material:
CNC machining offers a greater selection of materials that can be used to
create the parts. This can be very important deciding factor if a high-performance
plastic or a specific plastic is required. In general, harder plastics are
easier to machine than softer materials
For injected molded components, the material selection can be more limited. More and more high performing materials are being created with injection molding in mind. There are some materials which would be impossible to machine, but you can mold. Rubbers and other flexible materials would fall into this category.
Tolerance / Surface Finish:
Once again, the advantage goes to CNC machining. With most materials, a tighter
tolerance can be held, and a better surface finish can be obtained. One
advantage of injection molding is the repeatability from lot to lot. Molds can
last for millions of parts with minimal wear. This allows for the parts from
one batch to the next to be almost identical. With CNC machining, each part is made
on the machine to be created and more variability will be seen. Some of the
variability is due to different material lots, tools dulling before replacement,
even different employee’s might have ever so slightly allowable discrepancies but
still within tolerance.
Design:
First question should be; is the design going to change? If so, then you
might not want to spend the money to make a mold yet. Molds are difficult
and many times impossible to modify for changes in design.
But even before that, designing a part for machining can be much different than for molding. In both cases, one process can make features that would be difficult or impossible to create using the other process.
Machining allows for great flexibility in the design. Many features can be easily made with machining that would be very difficult or cost prohibited in molding. Some of these include, overhangs, large walls with no drafts and variable wall thicknesses.
On the other hand, injection molding allows for deep features, square holes and living hinges to be produced easily that could be difficult and expensive with machining.
As you can see, the decision between machining vs. injection molding is not straightforward. If you hadn't picked up on it, quantity is probably one of the most important factors...lower quantities aren't usually worth injection molding. But, If you need some of the advantages of both from tolerances, price and design features, you might want to consider a two-step operation where the main features of the part are injection molded and secondary machining options are done to perform the final steps. This is common technique to blend the benefits of the two processes together.
Hopefully this has been informative for you, please feel free to email me with any questions and I will try and answer your questions -
Ken Smith
Quality Systems Director
CrossWind Machining
ken@crosswindmachining.com
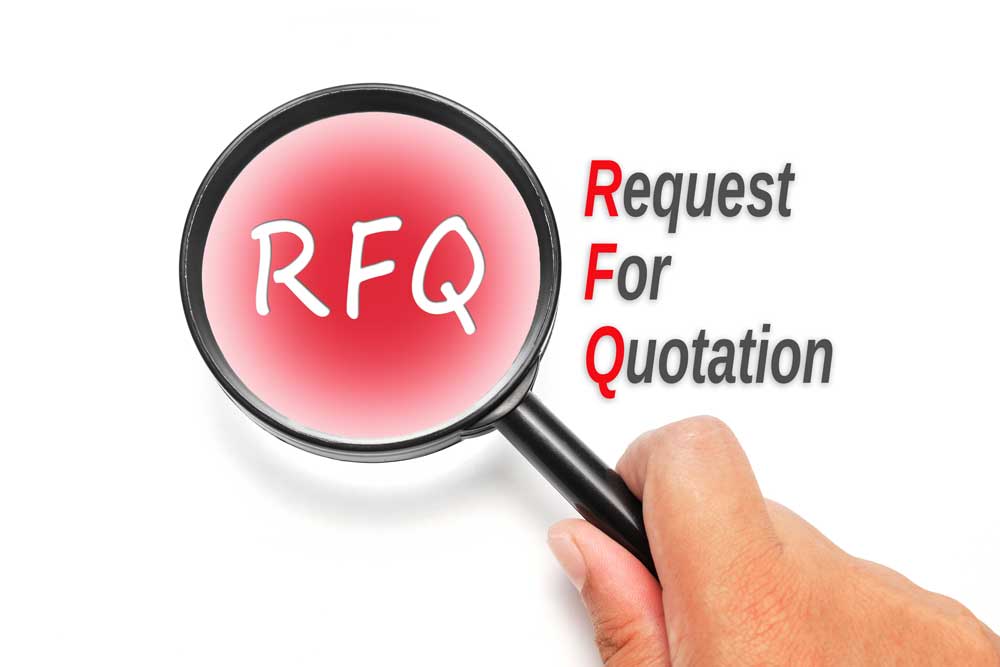
Here is a truth every job shop knows, and sometimes customers (potential and existing) seem to forget: Quoting isn’t free.
Preparing quotes is costly because it consumes the attention of knowledgeable staff members who could otherwise be giving attention (to existing) paying jobs.
Customers (potential and existing) want the best pricing and delivery times they can get, economics 101, right? The belief is that sending out RFQ’s (bids), will cause job shops to yield the lowest pricing they are willing to take to “win” the RFQ, thus providing the customer (buyer) his pick of RFQ responses with the lowest pricing available. The truth is, that is not always the case. Every shop is different when it comes to employees, availability, scheduling, capability, tooling, raw material availability & delivery, machinability and of course machines themselves, thus pricing may vary greatly. However, it is a necessary process to ensure your job schedule remains booked and securing the financial future of your business.
So, when CrossWind receives an RFQ, we (like everybody else I’m sure) have a process in which we go through to scrutinize each RFQ quickly, as to limit our time and resources spent on even deciding to respond to an RFQ. I should point out, that CrossWind DOES respond to EVERY RFQ that we get. However, the response may not be a bid, but rather an email or phone call stating that we are NOT bidding on the RFQ and a reason why we aren’t going to bid.
Please let me explain a bit further, for any shop to bid a project, they literally must sit down visualize the entire manufacturing of a single part from start to finish. Assuming we have the capability to do the part, CrossWind takes into consideration the following when quoting:
- Material costs and availability Including shipping time (get quotes?)
- Tooling costs and availability Including shipping time (get quotes?)
- Setup time for machining 1 part (which is the same for 500 or 5000 parts) – this may require multiple setups depending on what delivery schedule the client is asking for.
- 3rd party vendors needed (heat treating, anodization, laser etching, passivation, etc.) Inc. shipping costs & process times (get quotes?)
- Cycle time of making 1 part (which requires working through physically machining 1 part, and then we extrapolate for each quantity tier bid)
- Any special handling, cleaning or assembly of each part
- Any special instructions (i.e. packaging) on RFQ
- Delivery schedule requested
- Qty requested (5,50,500,5000?) (R&D or Production?)
- Is there a middleman involved (sales rep or bidding website)?
- Is this just an RFQ to check their current vendor of these parts or is it possible an order will come out of it.
Given these considerations, CrossWind’s RFQ process involves several people, so I want to make sure I’m not wasting valuable resources on an RFQ that we can’t even complete or meet expectations as the RFQ is requesting.
I won’t bore you with the internal process to get from RFQ request to an actual quote, but just know that an accurate bid takes at least an 1-2 hours to accurately complete, once you’ve got it started. Which is at least 1-2 hours @ $0 revenue for any resources used during that time, and many times we are waiting for quotes BACK for the quotes for material, tooling, 3rd party processes, etc. So realistically, it’s 1-2 days before you get all the information together to put it in an RFQ response back to the customer.
So, why am I explaining this you ask? Because I’d like our readers out there, sending out RFQ’s to multiple vendors (shops) to see that it takes time to put together an accurate quote on our end, and sometimes we may not have the time to complete the quote, or the part may not be a good fit for us to make, or we may see that we can’t make the delivery schedule you are asking for.
I also want to point out that “Economies of Scale” really come into play in bidding on RFQ’s…in laymen’s terms, the higher the quantity we’re bidding the lower the pricing per part. We amortize the cost of the entire job over the quantity bid per tier. That’s why 25 parts may cost you $27/each, but 250 parts may be $10/each and 2500 parts may be $7/each. The longer we can keep your parts on the machine, they cheaper they get…job shops like CrossWind Machining don’t make any money, unless the machines are making parts!
Lastly, don’t be offended if we ask you to “Price Point” the part (What are you currently paying for it?). We sometimes can tell you instantly that either we can’t beat the current price, or it will be close to what you are paying now. And it’s not worth the time and resources on our end to go through the exercise of verifying what we already knew, and not worth wasting your time waiting for an RFQ response that doesn’t do you any good.
I also want to point out, that when responding to an RFQ in which we’ve never made a component, we are basing our quoted pricing on mostly estimates of some those considerations…mainly cycle time & setup time. Once we get the job, the cycle time and setup times may vary from our estimates. So, we always look at the first time making a component as a learning curve, and maybe the cycle time and/or setup time is different than our estimate. Even though we are already bid at a certain price, the NEXT time the same component is asked to be bid on we may change the pricing…either up or down.
I hope this gives you some insight into what it takes on our end to figure out not only how much to quote when asked to do so, but the process and resources that go into just getting an accurate quote back to you so that CrossWind doesn’t lose money, but also we meet all of our clients specifications and delivery times needed.
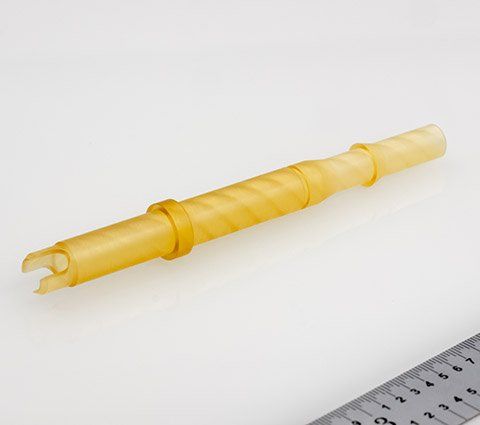
There are distinct advantages and applications for both CNC & CNC Swiss machines, but they are very different processes. Choosing which precision machining process depends on the specific job. Let me see if I can summarize them here for you.
CNC Swiss Machining
Swiss-type precision machining provides a cost-effective way to produce components for medical and defense products such as dust cover pins and firing pins used in military rifles. These long, slender components feature a tolerance band of 0.0005 inch on the part’s diameter.
A Swiss-type lathe consists of a variety of turning machines that feed the stock through a guide bushing. This means the OD turning tool can always cut the stock near the bushing, and therefore, near the point of support, no matter how long the workpiece. The machine feeds the work out of the spindle and past the tool as it goes. This makes the CNC Swiss-type particularly effective for long and slender turned parts.
Advantages of Swiss Turning Process
The advantage of a Swiss turning process is that the material is supported close to the tools that are cutting, using a guide bushing that the bar stock is pushed thru and into the tools. This prevents deflection of the bar stock when using a conventional turning process. On many machines, the tools are only a few thousands from the face of the guide bushing.
Swiss-Style Distinguishers
- Swiss-style screw machine, running off bar stock, typically creates a cylindrical part
- A 12-foot bar with automatic bar loaders in which 15-20 bars can be placed and fed through the machine
- The tools are machining as the bar is pushed forward through a guide bushing
- There are often numerous tools and multiple axes that can be used to complete the part
- Swiss machining can deal with complex designs and complex parts can be machined to completion on one machine
- Small runs from 1,000 pieces to high-volume production can be done through Swiss machining
- Processes can include drilling, turning, milling, boring, knurling, and many special processes
Swiss turning is ideal for long parts and small-diameter parts under .125″.
Examples of Swiss Parts Are:
- Contacts used in connectors
- Watch parts
- Shafts
- Long medical devices and implants
- A variety of connecting components for aerospace and electronics
CNC Conventional Machining
The first CNC precision machines were built in the 1940s and 50s and became the workhorses of the modern machine shop. Motion is controlled along multiple axes, normally at least two (X and Y), and a tool spindle that moves in the Z (depth). The position of the tool is driven by motors through a series of step-down gears, in order to provide highly accurate movements, or in modern designs, direct-drive stepper motor or servo motors. Open-loop controls work as long as the forces are kept small enough and speeds are not too great. On commercial metalworking machines, closed-loop controls are standard and required in order to provide the accuracy, speed, and repeatability demanded.
Advantages of Conventional Turning
Conventional turning extends the material from the chuck/collet to the overall length of the part, and then tools will move into the bar. Conventional turning is better suited for short, large-diameter parts with very tight tolerances. Conventional turning is also best suited for larger parts with difficult materials.
CNC-like systems are now used for any process that can be described as a series of movements and operations. These include laser cutting, welding, friction stir welding, ultrasonic welding, flame and plasma cutting, bending, spinning, hole-punching, pinning, gluing, fabric cutting, sewing, tape and fiber placement, routing, picking and placing (PnP), and sawing.
Conventional Turning Distinguishers
- CNC machining is ideal for forgings, castings, plates, or blocks of steel
- The use of higher production, special fixturing, and palletizing systems are created to facilitate the volume efficiently
- Tool changers in the machine store multiple tools, and the machine picks a tool for the operation, puts it back, picks the next tool and repeats the process until the product is machined to a finished state
- Fixtures can hold any number of parts from approximately one to 40
Examples of Conventional Turning Parts:
- Fluid controls
- Castings
- Automotive
- Anything with a diameter larger than 1.5″
I hope this sheds some light on some of the differences between conventional CNC (Lathes) & CNC Swiss (Lathes) Machining - it certainly helped me really understand which is the best to use in certain applications.
Ken Smith
Quality Systems Director
CrossWind Machining
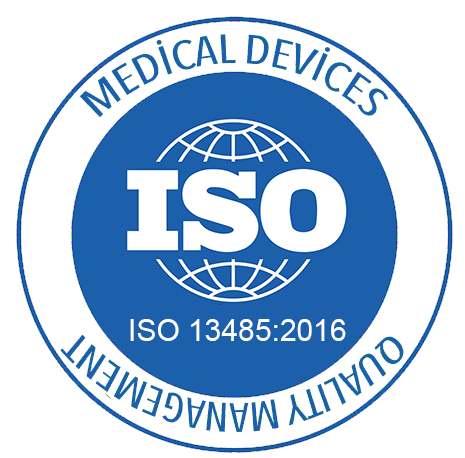
One particularly notable change with ISO 13485:2016 is the addition of more explicit risk management requirements. Companies will be required to consider the risk associated with a device from conception through its use. Device makers must plan and implement corrective action when problems are detected. Risk management must be incorporated into every aspect of the quality management system.
Suppliers like CrossWind Machining that are ISO 13485:2016 certified will be well-positioned to suit the needs of device makers. Although ISO 13485:2016 certification is not the only criterion companies should use in selecting a supplier, it is certainly an important one. ISO 13485:2016 also now carries FDA compliance at the higher level than every before. Device makers are responsible for the risk their suppliers contribute to their products and certification to this standard is a signal a supplier is committed to mitigating risk. So, if you're supplies are mitigating risk at every step of the manufacturing process, it certainly limits the risk with the final medical device product. It is my opinion that only a small portion of the suppliers will follow through with the ISO 13485:2016 certification, and roll back to ISO 9000 guidelines which are NOT medical device specific (and extremely "loose"), thus leaving medical device manufacturers at a much higher risk by using those suppliers. Can you really afford that type of risk?
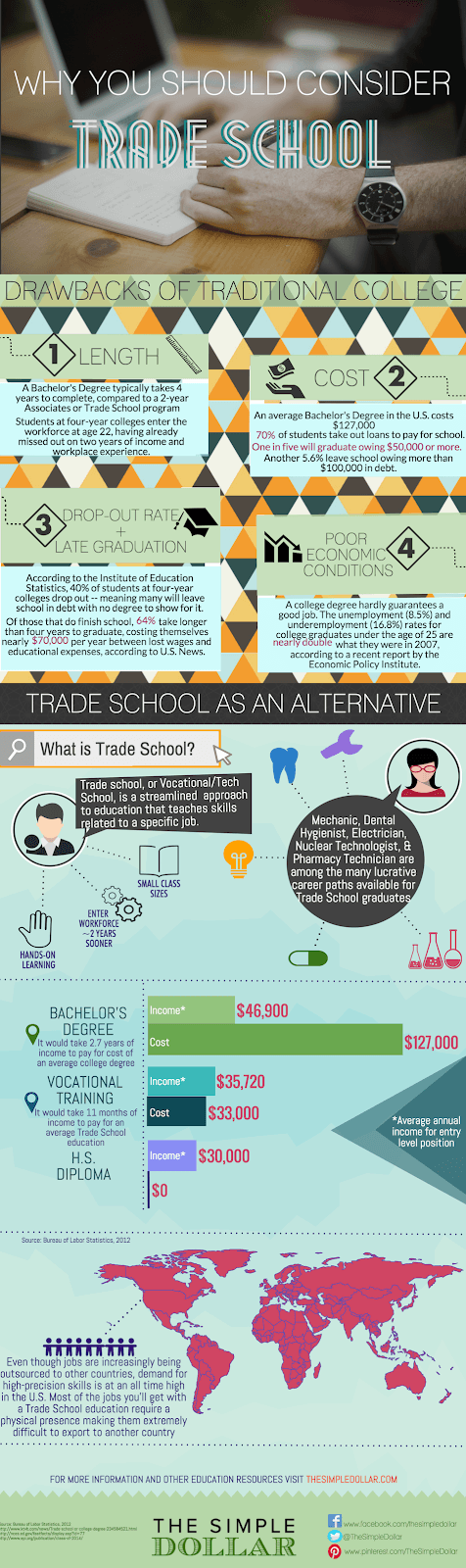